全员生产维护(TPM)
当前位置: 首页>>质量管理服务>>全员生产维护(TPM)企业全员生产生产维护(TPM)流程介绍
什么是全员生产生产维护(TPM)?
全员生产生产维护(TPM)是一种生产维护工作流程,可看作是针对于机器的“医疗技术”。其目的就是要明显地提高生产率,加强员工的士气和工作幸福感。TPM使生产维护成为了企业经营中十分必要和关键的核心,而不再被看作是无利可图的活动。生产维护停工期按计划被安排为工作日的一部分,在某些情况下甚至可作为生产过程的一个完整部分。这样做的目的就是为了将意外情况发生概率和非计划生产维护工作状况降到最低限度。
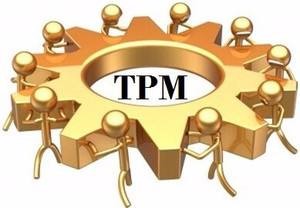
1.2 为什么要实行TPM?
引入TPM主要是为了达到如下目标:
a.降低成本;
b.用尽可能快的时间进行小批量生产;
c.在快速运行的经济环境下避免浪费;
d.在不降低产品质量的情况下缩短产品生产周期;
e.出售无缺陷产品给顾客。
1.3 TPM与TQM
TPM工作流程与当前流行的全面质量管理(TQM)工作流程是相当类似的。许多在TQM中应用的工具用于实现和优化TPM,如员工授权、建立基准、文档等等。二者的相同点如下;
1.都需要高层管理者的全面授权;
2.员工必须被授权才能进行纠错活动;
3.二者均是长期作业,TPM可能需要一年或更长的时间进行贯彻,并且是一个持续进行的过程。员工心中对工作责任感的积累也需要时间。
1.4 TPM的历史
TPM是由日本提出的一种理论。TPM的起源可追溯到1951年,预防性生产维护刚从美国介绍到日本。1960年,Nippondenso成为第一家在企业广泛应用预防性生产维护技术的公司。预防性生产维护理论强调,生产人员使用机器制造产品,而生产维护人员致力于维护这些机器,但是由于Nippondenso公司的自动程度较高,导致生产维护人员缺乏,使生产维护成为一个难题。所以管理人员决定由生产人员来负责设备的日常维护(这是一种自治性生产维护活动,是TPM的一个特点),而生产维护人员只需要执行一些必要的生产维护工作。
1.5 企业进行TPM的具体目标:
OPE(整体企业效能)至少达到80%;
OEE(整体设备效能)至少达到90%;
生产成本降低30%;
向客户发送货物时达到100%的成功率;
能够应对突发情况;
提议的数量增长3倍,培养一批具有多技能和高适应力的工人。
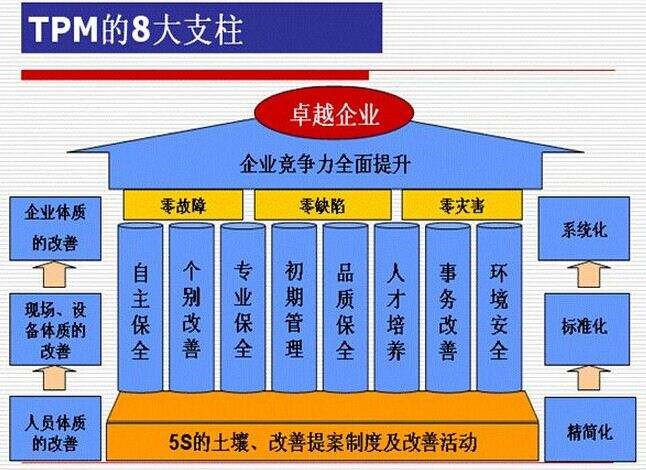
2.企业中引进TPM的步骤
阶段A——准备阶段
步骤1——管理者向全体人员宣布企业将引进TPM
在该阶段高层管理者的正确理解、承担任务和积极参与是非常必要的。当向全体人员宣布后,高级管理者应当了解工作流程。在内部刊物上公布,在黑板上公布。如果必要的话可以给所有的相关人员发一封信。
步骤2——进行TPM方面针对性培训
根据需要安排培训工作。某些人需要深入培训,而某些人只需要了解这一概念。带领相关人员去成功实施TPM的地方参观。
步骤3——建立TPM和部门委员会
TPM包括改进、自治生产维护、质量维护等工作。当委员会建立后,它应当关注这些需求。
步骤4——建立TPM工作体系和目标
为了成功,每个领域应该都建立标准,并制定目标。
步骤5——使其制度化的总体计划
当TPM成为一种企业文化后,下一步就应当采取措施使其制度化。通过预防性生产维护(PM)获得效益就证明已经达到了一个令人满意的水平。
步骤B——引进阶段
举行一个仪式并邀请所有的人员。供应者知道我们需要从他们那里获得合格产品。有可能我们客户和兄弟单位的相关公司和附属公司对此也很关注。有些人将会向我们学习,有些人将会帮助我们。由于我们对产品质量问题的关注,顾客将会与我们保持联系。
阶段C——执行
在该阶段有八项活动需要执行,这些活动被称之为实施TPM活动的八大支柱。这些活动中有四项是关于建立生产效率体系的,一项是关于新产品和设备的基本控制体系的,一项是关于提高管理层效率的,一项是对于安全、卫生等工作环境问题的控制。
阶段D——制度化阶段
到该阶段所有的相关活动都进入成熟时期。现在就是我们从预防性生产维护(PM)中获得效益的时候了。同时考虑一下在你采取该活动时所达到的挑战性水平。
我们的服务流程 :
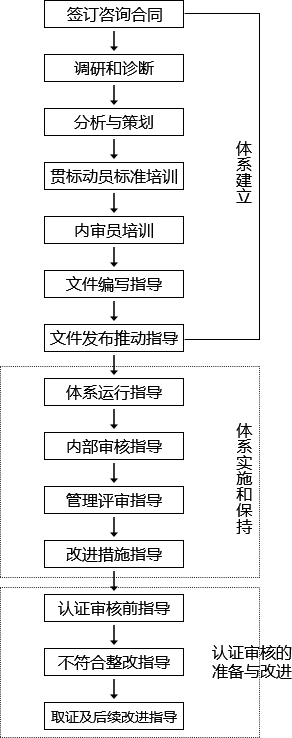
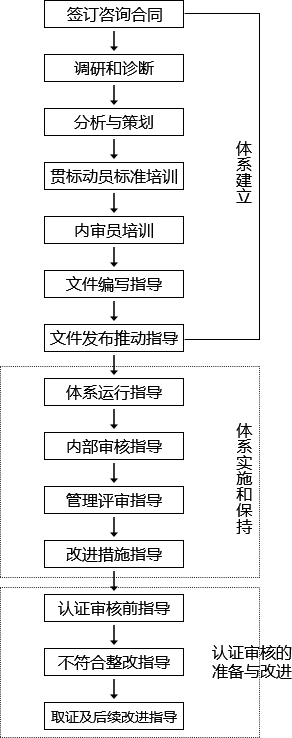